Содержание страницы
Современное металлообрабатывающее производство ставит высочайшие требования к точности и повторяемости изготавливаемых деталей. С появлением станков с числовым программным управлением (ЧПУ) скорость обработки выросла в разы, однако это обнажило и новые технологические вызовы. Одним из ключевых барьеров на пути к максимальной эффективности стала проблема контроля размеров непосредственно в процессе изготовления, особенно при работе с нежесткими или тонкостенными деталями. Решением этой задачи стало внедрение станочных измерительных систем (СИС), которые интегрируют функции контроля и измерения напрямую в технологический цикл станка.
Проблема деформации и погрешностей: почему традиционные методы неэффективны?
Для целого ряда отраслей, от аэрокосмической до приборостроительной, характерна обработка деталей со сложной геометрией и низкой жесткостью. Ключевая проблема таких изделий заключается в том, что после снятия сил закрепления (например, при разжатии тисков или патрона) происходит их упругая деформация. Это явление, вызванное перераспределением внутренних напряжений, накопленных в процессе резания, наглядно показано на рисунке 1. В результате геометрические параметры детали в свободном состоянии могут существенно отличаться от тех, что были измерены в зажатом.
Однако проблема контроля актуальна не только для нежестких деталей. Существует ряд других факторов, вносящих погрешность и требующих постоянной коррекции:
- Погрешность базирования инструмента: Инструментальные оправки с конусами, такими как 7:24 (известные как NC, BT, SK), несмотря на свою распространенность, имеют собственную погрешность базирования. Согласно ГОСТ 25827-2014 «Хвостовики инструментов с конусом 7:24 для ручной и автоматической смены инструмента.», суммарная погрешность установки инструмента в шпиндель может достигать 0,02-0,04 мм и более, что часто превышает допуск на выполняемый размер. Это вынуждает оператора производить «пристрелку» и ручную коррекцию вылета инструмента по оси Z после каждой его смены.
- Износ и смена режущих пластин: На станках токарной группы каждая смена или даже поворот неперетачиваемой твердосплавной пластины требует внесения новой коррекции. Допуски на изготовление самих пластин, даже прецизионных, могут быть сопоставимы с полем допуска на обрабатываемую поверхность, что регламентируется стандартами, например, ГОСТ 25346-2013 «Основные нормы взаимозаменяемости. ЕСДП».
Именно совокупность этих факторов и послужила мощным стимулом для разработки и массового внедрения автоматизированных станочных измерительных систем.
Архитектура и компоненты станочной измерительной системы
Современная станочная измерительная система представляет собой комплекс аппаратных и программных средств, глубоко интегрированных в систему управления станка. Типовая структурная схема такой системы показана на рисунке 2.
- Контактный измерительный датчик (щуп): Устройство для определения координат поверхностей заготовки и готовой детали.
- Датчик привязки инструмента (нулевого отсчета): Предназначен для точного измерения геометрии режущего инструмента (длины и диаметра).
- Интерфейс и приемник сигналов: Обеспечивают связь между датчиками и системой ЧПУ станка.
- Программно-математическое обеспечение (ПМО): Набор измерительных циклов и алгоритмов, которые управляют процессом измерений и обработки данных. ПМО может быть как стандартной частью СЧПУ, так и поставляться производителем измерительных систем (например, Renishaw, Heidenhain, Blum-Novotest).
Такими системами сегодня могут оснащаться практически все виды современного металлорежущего оборудования:
- Многоцелевые фрезерные и расточные станки;
- Шлифовальные и заточные станки;
- Зубообрабатывающие центры;
- Многоцелевые токарные и токарно-фрезерные станки.
Виды и функции измерительных датчиков
Датчики привязки инструмента (нулевого отсчета)
Эти устройства являются «точкой отсчета» для всего режущего инструмента в станке. Они могут быть как контактными, так и бесконтактными (лазерными), и выполняют ряд критически важных функций:
- Автоматическое измерение длины и диаметра инструмента: Исключает ошибки ручного ввода и сокращает время наладки.
- Расчет и ввод коррекции на инструмент: Система ЧПУ автоматически получает точные данные и записывает их в таблицу корректоров.
- Обнаружение поломки инструмента в процессе обработки: Лазерные системы позволяют на высокой скорости проверить целостность инструмента между операциями, предотвращая брак.
- Измерение биения режущих кромок и динамического износа: Позволяет оценить состояние инструмента в динамике, на рабочих оборотах.
- Проверка качества балансировки инструментальной оправки: Функция, доступная в наиболее продвинутых лазерных системах.
Курсивом в списке выделены уникальные возможности, присущие в основном бесконтактным лазерным датчикам. Примеры различных датчиков привязки инструмента показаны на рисунках 3-5.
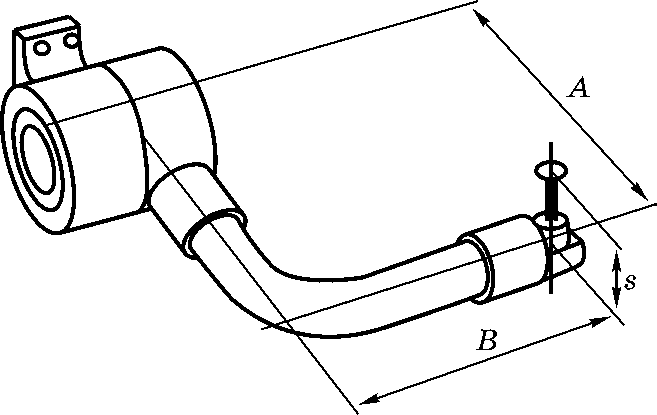
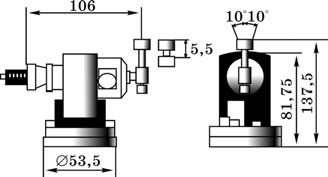
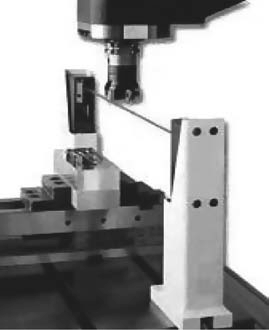
На станках, оснащенных контактными датчиками привязки, для контроля поломки инструмента могут дополнительно применяться специализированные лазерные барьеры (рис. 6). Инструмент периодически перемещается через лазерный луч, и если луч не прерывается, система фиксирует поломку и останавливает обработку.
Контактные измерительные датчики (щупы)
Эти датчики являются основным инструментом для работы с заготовкой. Они применяются для решения следующих задач:
- Привязка системы координат заготовки (WCS): Автоматическое определение положения детали на рабочем столе, что исключает длительное ручное выравнивание с помощью индикаторов и позволяет использовать более простые крепежные приспособления.
- Измерения в процессе обработки: Контроль размеров после черновых или получистовых проходов и автоматическое внесение коррекций в управляющую программу для достижения максимальной точности на чистовом проходе.
- Контроль первой детали из партии: Быстрая проверка соответствия детали чертежу перед запуском серийного производства.
- Финальный контроль нежестких деталей: Проведение всех ответственных измерений непосредственно на станке, до снятия зажимных усилий.
Конструкция типичного контактного датчика (рис. 7) включает измерительный щуп (стилус) и высокоточный механизм, регистрирующий его отклонение при касании поверхности. В процессе измерения датчик перемещается со скоростью подачи до 480 мм/мин. Для защиты от повреждений при случайных столкновениях предусмотрена угловая и осевая подвижность щупа, а при грубых ударах механизм защищает специальный срезной штифт.
- По проводной линии связи: Самый надежный, но ограничивает перемещение и автоматическую смену датчика.
- Модулированным оптическим (инфракрасным) лучом: Популярный метод, требующий прямой видимости между датчиком и приемником.
- По радиоканалу: Наиболее гибкий способ, не требующий прямой видимости и подходящий для крупных станков со сложной рабочей зоной.
- Индуктивным методом: Применяется в основном на токарных станках для датчиков, установленных в револьверной головке.
Программное обеспечение и типовые циклы измерений
Эффективность аппаратной части системы напрямую зависит от ее программного обеспечения. ПМО современных СЧПУ включает в себя обширную библиотеку стандартных измерительных циклов (например, по стандартам G400–G415), которые могут вызываться как в ручном режиме (MDI), так и непосредственно из управляющей программы.
Схема выполнения одного из таких циклов показана на рисунке 8.
- Калибровка измерительного щупа: Определение точного эффективного радиуса и длины щупа для компенсации его геометрии при измерениях (рис. 9, 10).
- Определение угла поворота системы координат: Выравнивание осей программы по фактическому положению заготовки на столе (рис. 11, 16).
- Назначение опорной точки (нуля программы): Определение центра отверстия, пересечения плоскостей, оси симметрии в качестве начала системы координат (рис. 12, 13, 14, 15, 17, 18).
Эти циклы позволяют полностью автоматизировать процесс «привязки» заготовки, даже если она установлена с произвольным смещением и поворотом относительно осей станка.
Рис. 9. Калибровка датчика по высоте
Рис. 10. Калибровка датчика по радиусу
Рис. 11. Определение угла поворота по прямой или пазу
Рис. 12. Назначение опорной точки на произвольно выбранной оси
Рис. 13. Назначение внешнего или внутреннего угла в качестве опорной точки
Рис. 14. Назначение центра кармана в качестве опорной точки
Рис. 15. Назначение оси симметрии в качестве опорной точки
Рис. 16. Определение угла поворота по двум отверстиям
Рис. 17. Определение опорной точки по четырем отверстиям
Рис. 18. Назначение центра окружности в качестве опорной точки через три отверстия
Заключение: Стратегические преимущества и взгляд в будущее
Внедрение станочных измерительных систем — это не просто модернизация, а качественный скачок в культуре производства. Быстрые и надежные контактные измерения с автоматическим обновлением коррекций станка позволяют добиться целого ряда стратегических преимуществ:
- Повышение точности и стабильности: Активное управление процессом обработки за счет постоянной обратной связи минимизирует влияние износа инструмента, температурных деформаций и погрешностей базирования.
- Сокращение брака и времени наладки: Автоматизация привязки заготовки и инструмента исключает до 90% ошибок, связанных с человеческим фактором, и значительно ускоряет подготовку станка к работе.
- Отказ от дорогостоящей оснастки: Отпадает необходимость в сложных и дорогих приспособлениях с точным механическим базированием, так как система сама находит положение детали в пространстве.
- Переход к безлюдному производству (Lights-Out Manufacturing): Возможность автоматического контроля и коррекции является ключевым элементом для организации работы в полностью автоматическом режиме.
В контексте Индустрии 4.0 станочные измерительные системы становятся неотъемлемой частью «умного производства». Данные, получаемые от датчиков, могут использоваться для создания цифровых двойников, предиктивного анализа состояния инструмента и адаптивного управления обработкой, когда станок в реальном времени корректирует режимы резания и траекторию на основе полученных измерений. Таким образом, СИС превращают станок с ЧПУ из простого исполнителя управляющих программ в интеллектуальную производственную единицу, способную самостоятельно обеспечивать высочайшее качество продукции.