Содержание страницы
Литейные сплавы цветных металлов занимают важнейшее место в современном материаловедении и машиностроении. Благодаря сочетанию высокой технологичности, коррозионной стойкости, малой плотности и широкого диапазона физических и механических свойств, такие сплавы находят применение в самых разных отраслях — от авиастроения и автомобилестроения до медицины и электроники.
Цветные металлы, в отличие от черных, не содержат значительных количеств железа, что придаёт им уникальные свойства и позволяет использовать их в условиях, где железо было бы неэффективным или даже разрушительным.
История использования цветных металлов уходит в глубокую древность. Ещё в III тысячелетии до нашей эры люди начали использовать медь и бронзу — сплав меди с оловом. Это положило начало бронзовому веку, важнейшему этапу в развитии человеческой цивилизации. Позже был открыт цинк и стал применяться для получения латуни, обладающей повышенной прочностью и стойкостью к коррозии. Алюминий был открыт лишь в XIX веке, но уже к середине XX века занял лидирующие позиции в авиастроении и электротехнике благодаря своей лёгкости и пластичности.
Развитие технологий литейного производства сделало возможным создание сложных по форме и структуре отливок из различных цветных сплавов. Магниевые и титановые сплавы, разработанные в XX веке, дали новые возможности для снижения массы конструкций, особенно в авиа— и ракетостроении. Никель и его сплавы стали основой для создания жаропрочных материалов, применяемых в условиях высоких температур.
1. Алюминиевые сплавы
Алюминиевые литейные сплавы обладают рядом выдающихся характеристик, среди которых высокая удельная прочность (σ / ρ), значительно превосходящая характеристики углеродистых сталей. Они также демонстрируют отличные показатели коррозионной стойкости, а также высокие тепло- и электропроводность. Эти уникальные свойства стали основой для широкого использования алюминиевых сплавов в различных отраслях, особенно в таких сферах, как авиационная промышленность и автомобилестроение.
Одним из важных факторов их популярности является отличная технологичность, что обеспечивает лёгкость обработки. Эти характеристики в полной мере объясняют применимость алюминиевых сплавов во множестве промышленных областей. В частности, можно отметить сплавы, которые отлично подходят для высокотехнологичного литья.
Группировка литейных алюминиевых сплавов представлена в ГОСТ 1583-93. Сплавы делятся на пять основных групп, каждая из которых имеет свой химический состав и механические свойства, приведённые в таблице 1 (прил. 1). Состав классификации следующий:
- I – сплавы на основе системы Al-Si-Mg;
- II – сплавы на основе системы Al-Si-Cu;
- III – сплавы на основе системы Al-Cu;
- IV – сплавы на основе системы Al-Mg;
- V – сплавы на основе системы Аl-Э (прочие элементы, являющиеся компонентами сплава).
Наиболее распространёнными являются сплавы I и II группы, которые называют «силуминами». Эти сплавы подразделяются на простые (АЛ2) и специальные силумины, которые дополнительно содержат магний (Mg) в незначительных долях или магний с медью (Cu). Для изготовления отливок применяются как доэвтектические (с содержанием кремния до 9 %) и заэвтектические (с содержанием кремния до 25 %) сплавы, как показано на рис. 1.
При этом можно отметить, что диаграмма фазового равновесия системы Al-Si демонстрирует эвтектическое соединение с содержанием 11,7% кремния, где происходит образование твердого раствора кремния в алюминии. Важно, что максимальная растворимость кремния в алюминии составляет 1,65% при температуре эвтектики, которая равна 577°C. Со временем, с увеличением содержания кремния в доэвтектических сплавах, в структуре сплавов возрастает количество эвтектики, что положительно сказывается на литейных свойствах.
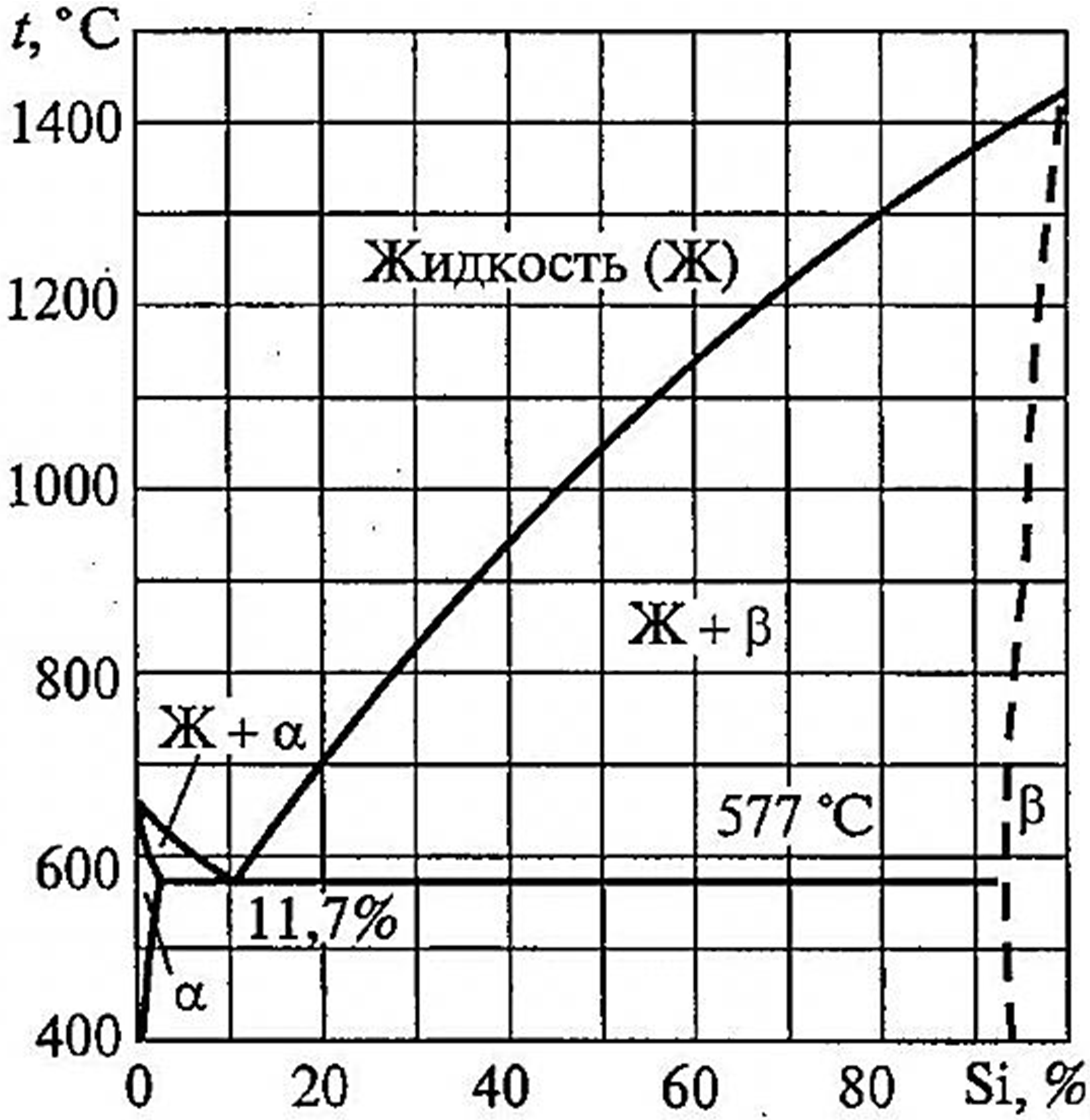
Алюминиевые сплавы, принадлежащие к доэвтектическим категориям, обычно характеризуются дендритной структурой, где твёрдый раствор кремния в алюминии и эвтектика присутствуют одновременно. Тем не менее, крупные пластинки кремния, которые могут появляться в эвтектике, оказываются концентраторами напряжений, что ухудшает пластичность материала. Для минимизации таких недостатков применяются различные методы модификации, например, добавление солей натрия (NaF + NaCl), что позволяет измельчить кремниевые включения.
Тем не менее, если содержание кремния в сплаве менее 8%, применение модификации становится экономически нецелесообразным, так как влияние данного процесса на улучшение свойств является минимальным и часто не оправдывает затрат, особенно при воздействии охлаждения.
Одним из ключевых факторов, определяющих литейные свойства алюминиевых сплавов, является интервал кристаллизации. Сплавы I и II групп, как правило, имеют более узкий интервал кристаллизации, не превышающий 50°C. Это придаёт им высокую жидкотекучесть и хорошую стойкость к образованию трещин как горячих, так и холодных. Однако такие сплавы склонны к образованию усадочных раковин. В противоположность этим сплавам, другие группы, такие как III, IV и V, имеют гораздо более широкий интервал кристаллизации, что снижает их жидкотекучесть и делает их более подверженными образованию горячих трещин и пористости.
В частности, алюминиевые сплавы, содержащие магний (IV группа), склонны к образованию газовой и газоусадочной пористости, что может быть особенно заметно при литье в металлические формы. Именно поэтому для таких сплавов был разработан метод литья в автоклаве, который позволяет значительно снизить газовую пористость и повысить плотность отливок.
Кроме того, расплав алюминия при литье имеет повышенную склонность к окислению, что приводит к образованию неметаллических включений и оксидных пленок. Эти явления требуют применения дополнительных процессов, таких как дегазация и фильтрация расплавов, а также тщательного проектирования литниковых систем, чтобы обеспечить спокойное и равномерное заполнение форм.
2. Сплавы на основе меди
Медь — это пластичный металл с высокой плотностью 8950 кг/м3, а ее температура плавления составляет 1083 °С. Она нашла широкое применение в промышленности благодаря своим отличным характеристикам, таким как высокая химическая устойчивость, теплопроводность, электропроводность и износостойкость. Медь и ее сплавы с древних времен активно используются в художественном литье благодаря своей жидкотекучести.
В современной технике используется множество различных медных сплавов, включая двойные, тройные и многокомпонентные. Основные элементы, входящие в состав медных сплавов, включают олово, цинк, свинец, алюминий, марганец, кремний, бериллий, никель, железо, хром, фосфор, титан, золото, серебро и другие.
Медные сплавы классифицируются на две большие группы: бронзы и латуни.
Сплавы меди с элементами, помимо цинка и никеля, относят к бронзам. Ранее бронзами называли только сплавы меди с оловом, однако сегодня такие сплавы могут содержать и другие элементы. Бронзы, не включающие олово, называются безоловянными. Латуни же являются сплавами меди с цинком (до 50 %), с добавлением небольшого количества других элементов. Применяются для их маркировки буквы «Бр» для бронз и «Л» для латуней, за которыми следуют элементы и цифры, показывающие их процентное содержание в сплаве.
Элементы, использующиеся в медных сплавах, обозначаются так:
- О – олово,
- А – алюминий,
- Ц – цинк,
- К – кремний,
- Ф – фосфор,
- С – свинец,
- Ж – железо,
- Мц – марганец,
- Н – никель.
К примеру, маркировка БрА7Мц15Ж3Н2Ц2Л обозначает бронзу, содержащую 7 % алюминия, 15 % марганца, 3 % железа, 2 % никеля, 2 % цинка, а остальная часть — это медь. Марка ЛЦ40Мц3Ж обозначает латунь с 40 % цинка, 3 % марганца и до 1,5 % железа, остальное — медь. Буква «Л» в конце маркировки указывает на литейный состав, отличающийся от деформируемой бронзы с аналогичным химическим составом.
Литейные бронзы
Механические свойства литейных бронз по ГОСТ 613-79 представлены в следующей таблице:
Таблица 1. Механические свойства бронз
Группа бронз | Марка сплава | Суммарное содержание упрочняющих легирующих элементов, % |
Механические свойства, не менее |
||
σв, Н/мм2 | δ, % | НВ | |||
Оловянные и оловянно-цинковые | Бр08Ц4 | 12 | 196 | 10 | 75 |
Бр010Ц2 | 12 | 225 | 10 | 75 | |
Бр010Фl | 11 | 245 | 3 | 90 | |
Оловянно-цинково-свинцовые | БрО4Ц4С17 | 8 | 147 | 12 | 60 |
БрО5Ц5С5 | 10 | 176 | 4 | 60 | |
БрО3Ц12С5 | 15 | 206 | 5 | 60 | |
Свинцовые и оловянно-свинцовые | БрС30 | 0 | 59 | 4 | 25 |
Бр05С25 | 5 | 137 | 6 | 60 | |
Бр010С10 | 10 | 196 | 6 | 78 | |
Алюминиевые | БрА9Мц2Л | 11 | 392 | 20 | 80 |
БрА10Мц2Л | 12 | 490 | 12 | 110 | |
БрА10Ж3Мц2 | 15 | 490 | 12 | 120 | |
БрА10Ж4Н4Л | 18 | 578 | 6 | 170 | |
БрА11Ж6Н6 | 23 | 578 | 2 | 250 | |
БрА7Мц15Ж3Н2Ц2 | 29 | 607 | 18 | – |
Согласно таблице, приведенной в ГОСТ 613-79 и ГОСТ 493-79, механические свойства сплавов изменяются при литье в различные формы: в кокиль и песчаные формы. Для оловянных бронз при литье в песчаные формы прочность σв может быть снижена на 20–40 Н/мм2, а для алюминиевых — на 40–100 Н/мм2.
Основной компонент оловянных бронз — олово, содержание которого варьируется от 3 до 10 %. При температуре эвтектики (798 °С) максимальная растворимость олова в меди составляет 13,5 %. Структура бронз с меньшим содержанием олова представлена твердым раствором дендритного строения с неоднородным распределением компонентов. Бронзы с содержанием олова выше 8 % имеют структуру, состоящую из α-фазы и эвтектоида (α + Cu3Sn8), что повышает их твердость и прочность.
Для снижения расхода олова в сплавы добавляют цинк (2–12 %), который растворяется в меди, повышая прочностные свойства и улучшая литейные характеристики. Примеры таких сплавов — это пушечные бронзы, содержащие около 6 % Sn и 3 % Zn, а также 5 % Sn и 5 % Zn, используемые как антифрикционные материалы.
Также в состав оловянных бронз часто вводят свинец, который улучшает их антифрикционные свойства. Свинец образует в структуре сплава выделения, которые снижают механические свойства, но обеспечивают хорошую прирабатываемость.
Безоловянные бронзы (или специальные) содержат такие легирующие элементы, как алюминий, марганец, кремний и другие. Например, в свинцовой бронзе БрС30 свинец выполняет такую же функцию, как и в оловянно-свинцовых бронзах, улучшая антифрикционные качества. В алюминиевых бронзах (с 5–12 % Al) прочность и твердость увеличиваются с ростом содержания алюминия, а ударная вязкость и удлинение уменьшаются из-за образования интерметаллида Cu3Al.
Алюминиевые бронзы обладают высокими антифрикционными свойствами и коррозионной стойкостью в различных условиях, включая атмосферу, морскую воду и органические кислоты. Эти сплавы морозостойки и немагнитны, а также не искрят при ударе. Добавление железа, марганца и никеля способствует улучшению их прочностных характеристик.
Латуни являются медными сплавами, которые делятся на двойные (простые) и специальные, включающие добавки Fe, Mn, Ni, Si, Sn, Рb. Этот вид сплавов характеризуется важными свойствами, которые значительно зависят от состава добавок.
Цинк растворяется в меди в рамках раствора замещения, при этом до концентрации Ср = 39 %. При превышении этой величины (более 39 %) образуется βр-фаза, представляющая собой твердый раствор на основе соединения CuZn. Однофазные β-латуни обладают наибольшей пластичностью, но при этом имеют меньшую прочность. Эти сплавы обычно применяются в обработке давлением. Свойства латуней с добавлением цинка меняются, аналогично тому, как это происходит с меди-алюминиевыми сплавами (Cu-Al).
Добавки железа и марганца в латунь также оказывают влияние, аналогичное их действию в сплавах Cu-Al: они способствуют измельчению зерна и увеличению прочности материала.
Для улучшения структуры медных сплавов, таких как бронзы и латунь, используется модификация с добавлением Mo, Nb, V и В в малых количествах, не превышающих 0,1 %.
Особенности литейных свойств медных сплавов заключаются в высокой жидкотекучести, что делает их подходящими для художественного литья. Сплавы, такие как БрО5Ц5С5, БрО6Ц6С3, ЛЦ20К3С3, часто применяются в этом процессе. При этом важным аспектом является не только литейная способность, но и декоративные, а также антикоррозионные качества этих сплавов. Один из ключевых факторов — это интервал кристаллизации сплавов. В таблице 2 представлены значения интервала кристаллизации для ряда бронз и латуней.
Таблица 2. Интервал кристаллизации бронз и латуней
Медный сплав | БрО10С10 | БрО8Ц4 | БрО5Ц5С5 | ЛЦ16К4 | ЛЦ40А1Ж1 | БрА10Ж1 |
Интервал кристаллизации | 167 | 150 | 145 | 96 | 17 | 8 |
Как и другие сплавы, медные сплавы можно классифицировать в зависимости от их интервала кристаллизации на три группы: с узким интервалом кристаллизации (8…50 °С, как, например, БрА10Ж1), с средним интервалом (50…100 °С, например, ЛЦ15К4), и с широким интервалом (>100 °C, например, БрО10С10).
Сплавы с широким интервалом кристаллизации обладают склонностью к рассеянной пористости, что затрудняет получение плотных и герметичных отливок. В то время как сплавы с узким интервалом кристаллизации формируют сосредоточенные усадочные раковины, которые легче корректируются на технологическом этапе. Линейная усадка медных сплавов обычно составляет от 1,5 % до 2,0 %.
Для медных сплавов с широким интервалом кристаллизации существует риск появления горячих трещин, особенно при использовании металлических форм. Однако они не склонны к образованию холодных трещин. В процессе плавки медных сплавов крайне важно минимизировать их насыщение газами, поскольку это может привести к образованию пористости. Например, в сплавах Cu-Sn и Cu-Sn-Pb газами, которые могут вызвать газовую пористость, являются О2, водяной пар, углекислый газ и сернистые соединения. Латуни с высоким содержанием цинка защищены от насыщения водородом с помощью паров цинка.
Для снижения газонасыщенности медных сплавов применяют методы дегазации, такие как продувка гексахлорэтаном (аналогичный метод используется для алюминиевых сплавов), вакуумирование и другие техники.
Кроме того, при плавке медных сплавов существует риск загрязнения сплава оксидными пленами и другими неметаллическими включениями. Для предотвращения этого некоторые сплавы, например, алюминиевые бронзы, проходят фильтрацию через керамические магнезитовые фильтры или металлические сетки из молибдена. При заливке сплава важно обеспечить плавное и равномерное заполнение формы с использованием расширяющихся литниковых систем.
Медные сплавы, такие как оловянные и алюминиевые бронзы, подвержены дендритной ликвации, а свинцовые бронзы — гравитационной ликвации, что также важно учитывать в процессе литья.
3. Магниевые сплавы
Магниевые сплавы широко применяются в авиастроении, ракетной технике и производстве транспортных машин благодаря своей низкой объемной массе и высокой удельной прочности, что позволяет значительно снизить массу двигателей, агрегатов и других узлов машин. Одним из ключевых достоинств магниевых сплавов является их способность эффективно поглощать механические вибрации.
Однако магниевые сплавы имеют ряд недостатков. В первую очередь, они значительно уступают алюминиевым сплавам по пластичности и коррозионной стойкости. Также они имеют высокую окисляемость в расплавленном состоянии и могут воспламеняться при температурах 400–550 °C, что затрудняет процесс изготовления отливок.
Литейные свойства магниевых сплавов достаточно низкие: они характеризуются недостаточной жидкотекучестью, большой линейной усадкой и склонностью к образованию усадочных рыхлот и горячих трещин.
Литейные магниевые сплавы обычно обозначаются буквами МЛ (магниевый, литейный) и цифрами, которые указывают на номер сплава, например, МЛ5, МЛ6, МЛ8.
В зависимости от химического состава магниевые сплавы делятся на три основные группы:
- I – сплавы на основе системы Mg-Al-Zn;
- II – Mg-Zn-Zr;
- III – Mg-РЗЭ-Zr (РЗЭ – редкоземельные элементы).
Наиболее популярными магниевыми сплавами с хорошими литейными свойствами являются сплавы системы Mg-Al-Zn, такие как МЛ5 и МЛ6. Эти сплавы относятся к высокопрочным материалам с пределом прочности σв < 220 МПа и применяются для изготовления деталей, работающих при нагрузках в двигателях автомобилей и самолетов с рабочими температурами до 150 °C. Сплав МЛ4, обладающий высокой коррозионной стойкостью, склонен к микропористости и образованию горячих трещин.
В отличие от сплавов системы Mg-Al-Zn, сплавы системы Mg-Zn-Zr имеют более высокие прочностные характеристики (σв = 220–250 МПа), меньшую чувствительность к микрорыхлотам и лучшее влияние на механические свойства. Типичным примером этого типа является сплав МЛ12, который отличается повышенной пластичностью, лучшей коррозионной стойкостью и отличными литейными свойствами. Легирование цирконием улучшает жаропрочность сплава.
Сплавы системы Mg-РЗЭ-Zr (МЛ9, МЛ10, МЛ11, МЛ19) являются жаропрочными и могут работать при температуре до 250–300 °C в течение длительного времени и до 400 °C кратковременно. Основными легирующими элементами в этих сплавах являются неодим (для МЛ9, МЛ10, МЛ19) и цериевый мишметалл (для МЛ11). Все сплавы этой группы также легированы цирконием и обладают хорошими литейными и технологическими свойствами.
Особенности плавки магниевых сплавов
Магниевые сплавы имеют высокую реакционную способность в расплавленном состоянии. Они легко образуют соединения с кислородом и азотом воздуха, а также разлагают пары воды и поглощают водород. Поэтому плавка магниевых сплавов проводится в тигельных печах под слоем флюса, который плавится при более низкой температуре и создаёт защитный слой, предотвращающий контакт жидкого металла с атмосферным воздухом. Также используют специальные печи с отсутствием доступа воздуха.
Для выплавки магниевых сплавов используют стальные тигли, так как графитовые тигли подвержены разрушению флюсами, а шамотные тигли могут загрязнять сплав силицидом и оксидом магния.
Флюсы для плавки магниевых сплавов должны соответствовать следующим требованиям:
- Иметь температуру плавления ниже температуры выплавляемого сплава;
- Обладать высокой рафинирующей способностью (удалять из сплава оксиды и нитриды);
- Обладать высокой жидкотекучестью;
- Иметь большую плотность при температуре 750 °C, чем плотность магниевого сплава при этой же температуре.
При повышении температуры до 750 °C твердые неметаллические включения, такие как оксиды и нитриды, оседают на дно тигля. Для улучшения очищения расплава от этих включений металл следует обработать расплавленным флюсом и перемешать. При перегреве расплава до 850–900 °C вязкость металла уменьшается, что способствует оседанию флюса и измельчению структурных составляющих сплава, что, в свою очередь, улучшает механические свойства отливаемых деталей.
Также для повышения качества плавки магниевых сплавов используется метод модификации, введя углекислые кальция и магния.
В некоторых случаях плавку проводят в нейтральной атмосфере под газовым слоем аргона или в специальных печах закрытого типа с местной вентиляцией.
4. Титановые сплавы
Титановые сплавы — один из важнейших конструкционных материалов для отраслей, в которых предъявляются повышенные требования к прочности и устойчивости к агрессивным средам. Их отличает высокая удельная прочность (σв / ρ) при плотности 4500 кг/м3, что делает их особенно ценными в авиастроении, включая производство самолетов и вертолетов. Также они активно используются в химической и нефтеперерабатывающей промышленности, а также в черной и цветной металлургии. Здесь оправдана их высокая стоимость благодаря длительному сроку службы деталей, контактирующих с агрессивными веществами — за счёт образования на поверхности прочной пленки TiО2.
Характерной чертой этих сплавов является устойчивое поведение в агрессивных средах, что делает их идеальными для элементов оборудования, эксплуатируемых в экстремальных условиях. К примеру, они нашли применение в памятниках (например, памятник Ю. Гагарину в Москве), а также в спортивном инвентаре — таких, как гольф-клюшки.
По фазовой структуре титановые сплавы делятся на три типа:
- однофазные α-сплавы;
- двухфазные (α + β)-сплавы;
- однофазные β-сплавы.
0 10 20 30 %Al
Рис. 2. Диаграмма состояния Ti-Al
Основой большинства титановых сплавов выступает бинарная система Ti-Al (рис. 2), с варьирующимся содержанием алюминия от 2,6 до 7,0 %. Маркировка сплавов осуществляется через префикс «ВТ», далее следуют номер и буква «Л». Это отражено в таблице 3, где представлены химические составы различных литейных титановых сплавов.
Таблица 3. Химический состав литейных титановых сплавов, масс. %
Марка сплава | Al | Mo | V | Zr | Cr | Si | Sn | Fe |
ВТ5Л | 4,1–6,2 | – | – | – | – | – | – | – |
ВТ6Л | 5,0–6,5 | – | 3,5–4,5 | – | – | – | – | – |
ВТ31Л | 5,3–7,0 | 2,0–3,0 | – | – | 0,8–2,3 | 0,15–0,40 | – | 0,2–0,7 |
ВТ9Л | 5,6–7,0 | 2,8–3,8 | – | 0,8–2,0 | 0,8–2,0 | 0,20–0,35 | – | – |
ВТ14Л | 4,3–6,3 | 2,5–3,8 | 0,9–1,9 | – | – | – | – | – |
ВТ20Л | 5,5–6,8 | 0,5–2,0 | 0,8–1,8 | 1,5–2,5 | – | – | – | – |
ВТ21Л | 5,8–7,0 | 0,4–1,0 | 0,8–1,5 | 4,0–6,0 | 4,0–6,0 | – | – | – |
ВТ35Л | 2,6–3,6 | 0,2–1,0 | 14,8–15,8 | 0,2–0,8 | 2,5–3,5 | – | 2,5–3,5 | – |
ВТ5Л, ВТ20Л и ВТ21Л классифицируются как однофазные α-сплавы. К двухфазным (α + β) типам относятся ВТ6Л, ВТ31Л, ВТ9Л и ВТ14Л, отличающиеся наличием значительной доли β-фазы. Псевдо-β-сплавом является ВТ35Л.
Среди конструкционных материалов титановые сплавы выделяются высокой температурой плавления — температура ликвидуса колеблется в пределах 1620–1670 °С. При этом их теплопроводность существенно ниже — в 15 раз по сравнению с алюминием и в 4 раза по сравнению с железом.
При всей прочности титановые сплавы уступают по модулю упругости даже простым углеродистым сталям. Их высокая химическая активность требует применения специализированных методов производства, таких как гарнисажная вакуумно-дуговая плавка с использованием расходуемого титанового электрода. Формы, как правило, изготавливаются из графита, а заливку осуществляют в условиях вакуума на центробежных установках.
Модифицирование структуры затруднено из-за особенностей технологии, однако положительные результаты достигаются для малолегированных сплавов (ВТ5Л, ВТ6Л) при введении бора или карбида бора в количестве 0,007–0,01 %. Для сплавов типа ВТ9Л и ВТ12Л данный подход оказался неэффективен.
Титан склонен к образованию растворов внедрения с кислородом и азотом, но их избыток — свыше 0,12–0,20 % для O2 и 0,05 % для N2 — превращает их в вредные примеси. Водород также вреден: он быстро диффундирует в структуру и в больших количествах растворяется в твердом титане. Его удаляют посредством вакуумного отжига.
Однако эти особенности нашли применение: в водородной технологии литейного производства используется свойство титана насыщаться водородом и обратимо его терять. Это позволяет использовать Н2 как защитную среду, а также — для локального водородного охрупчивания с целью упрощения удаления литников.
Если содержание углерода в сплаве превышает 0,2 %, то он образует карбиды, снижающие прочность и ухудшающие обрабатываемость, которая и без того затруднена. Несмотря на это, жидкотекучесть у сплавов высокая, однако слабая свариваемость фронтов потоков вызывает дефекты неспаев.
Тепловые напряжения, возникающие при остывании, особенно выражены в отливках с переменной толщиной из-за слабой теплопроводности. Снятие напряжений достигается полным отжигом (для ВТ1Л, ВТ5Л, ВТ6Л и ВТ20Л — при 800 °С, ВТ9Л — при 940 °С) или неполным отжигом (600 °С) с эффектом до 70 %. Чтобы избежать коробления, в конструкцию вводят временные перемычки, которые удаляются после термической обработки.
5. Цинковые сплавы
Цинк в технически чистом виде демонстрирует приемлемые механические качества и легко поддается различным видам обработки: волочению, штамповке, прессованию и прокатке как в холодном состоянии, так и при нагреве до 130…170 °C. Металл характеризуется сравнительно высокой плотностью — 7130 кг/м3 в твердой фазе и 6810 кг/м3 в жидком виде, а также низкими температурами перехода: плавление происходит при 419,5 °C, а кипение — при 907 °C. Линейная усадка цинка при этом составляет порядка 1,6 %.
Существуют различные марки цинка, различающиеся по уровню содержания примесей. Например, марка ЦВОО характеризуется минимальным количеством посторонних элементов — менее 0,005 %, в то время как у марки Ц3 этот показатель не превышает 2,5 %. При обозначении сплавов применяется символ «Ц», за которым следуют буквы элементов, входящих в состав (например, А — алюминий, М — медь), и цифры, указывающие их процентную долю. Среди наиболее распространённых цинковых сплавов для литья под давлением — ЦА4 и ЦАМ4-1, а также антифрикционные литейные варианты — ЦАМ9-1,5Л и ЦАМ10-5Л.
ЦА4Л содержит 4,0 % алюминия. Его микроструктура представлена первичными кристаллами α-твердого раствора (содержание Al — до 1,1 %) и эвтектикой, формирующейся при температуре 382 °C, включающей кристаллы α- и β-твёрдых растворов. Хотя эвтектоидное превращение должно начинаться при 265 °C, в условиях быстрого охлаждения при литье под давлением оно блокируется. Однако при комнатной температуре постепенно реализуется так называемое «естественное старение».
Во время старения наблюдается снижение размеров заготовки (в среднем на 0,08 %), что может негативно сказаться на точности изделий. Для устранения этого эффекта применяют отжиг — нагрев до 100 °C и выдержку от 3 до 10 часов. Одной из важных особенностей цинковых сплавов Zn-Al является их подверженность межкристаллитной коррозии, особенно в присутствии примесей, таких как свинец, кадмий и олово. Их допустимые концентрации ограничиваются значениями, %: Pb — 0,015; Sn — 0,001; Cd — 0,003. В то же время добавление магния (Mg) способствует повышению устойчивости к коррозии и уменьшает объемную деформацию.
В сплаве ЦАМ4-1 к основному составу ЦА4 добавлена медь (1,0 %), находящаяся в твердом растворе, без образования дополнительных фаз. Это повышает его механические характеристики — прочность и твёрдость, что делает его более предпочтительным в различных отраслях. Данные сплавы нашли широкое применение в автомобильной промышленности: используются при изготовлении корпусов карбюраторов, насосов, декоративных и конструктивных элементов. Антифрикционные сплавы на основе цинка, как правило, включают в состав алюминий и медь, формируя тройные системы Zn-Al-Cu. Технологии литья включают методы под давлением, в кокиль и реже — в песчано-глинистые формы.
Цинковые сплавы отличаются высокой жидкотекучестью, обусловленной их узким интервалом плавления и низкой температурой плавления (Tпл). Благодаря этим свойствам обеспечивается высокая точность и детализация отливок, что делает такие сплавы актуальными для шрифтолитейного производства. Линейная усадка составляет 1,0–1,2 %. При использовании металлических форм необходимо учитывать склонность к образованию горячих трещин. Для минимизации дефектов литьё проводят в инертной атмосфере (азот), не допуская перегрева свыше 480 °C, что предотвращает насыщение газами и образование включений.
6. Никелевые сплавы
Никель — тяжелый цветной металл с плотностью 8900 кг/м3, температурой плавления 1452 °C и кипения 3000 °C. В технически чистом виде (99,5 %) он используется для получения слитков, а при добавлении легирующих элементов — для фасонных отливок. В состав таких сплавов входят: Si — 1,0–2,0 %, Mn — 1,0–1,5 %, C — менее 0,3 %, S — менее 0,03 %, Mg — 0,08–0,1 %, Fe — 1,0 % и Cu — до 0,3 %. Никель — важный компонент множества сплавов: инвар (Fe-Ni с 36 % Ni, КЛР ≈ 1,5·10–5 К–1), пермалой (Ni 80 %, отличается высокой магнитной проницаемостью), монетный мельхиор, нихром, а также жаропрочные композиции для лопаток газотурбинных установок.
Подобно чистому металлу, никелевые сплавы обладают высокой термической и химической устойчивостью: жаростойкостью, жаропрочностью и отличной коррозионной стойкостью.
Современная система маркировки никелевых литейных сплавов не унифицирована. Применяются различные схемы: например, по аналогии с легированными сталями — нихром Х20Н80, сплав ХН78Т, а также аббревиатуры с буквами и порядковыми номерами — ЖС3, Ж6, ЖС6К и др.
Никелевые сплавы, несмотря на относительно узкий температурный интервал кристаллизации, имеют высокую температуру ликвидуса, что обеспечивает приемлемую жидкотекучесть. В то же время они склонны к образованию усадочных раковин концентрированного характера. Линейная усадка составляет 1,9–2,0 %. Среди типичных дефектов отливок — горячие трещины, газовая пористость, неметаллические включения, пленки и проявления дендритной ликвации.
Изготовление отливок из жаропрочных никелевых сплавов требует использования передовых технологий: вакуумной плавки и заливки, направленной кристаллизации с формированием структуры в виде столбчатых зёрен. Это особенно важно для изделий, работающих в условиях экстремальных температур и напряжений, таких как лопатки турбин или элементы магнитных систем.
Интересные факты:
- Самый лёгкий литейный цветной сплав — магниевый. Плотность магния составляет всего 1730 кг/м³, что делает его незаменимым в производстве деталей, где особенно важна минимальная масса.
- Из алюминиевых сплавов отливаются корпуса современных смартфонов, а также части велосипедов, автомобилей и даже поездов. — Латунные отливки (сплав меди с цинком) обладают высокой декоративной ценностью и часто используются в производстве фурнитуры и предметов интерьера.
- Первый промышленный процесс получения алюминия назывался способом Холла-Эру, он был открыт одновременно двумя учёными — американцем Ч. Холлом и французом П. Эру в 1886 году.
- Несмотря на высокую стоимость, титановые сплавы применяются даже в медицине — для изготовления имплантатов и протезов, так как они биоинертны и не вызывают отторжения у организма.
Заключение
Литейные сплавы цветных металлов — это фундамент современной инженерии, позволяющий создавать прочные, долговечные и лёгкие изделия практически любой формы. Разнообразие цветных металлов и их сплавов предоставляет широкий выбор материалов под конкретные задачи в любой отрасли промышленности. Постоянное совершенствование технологий литья, в том числе вакуумного, центробежного и прецизионного, открывает новые горизонты в разработке сплавов с особыми свойствами. Современное материаловедение делает ставку на экологичность, экономичность и многофункциональность, в чём цветные литейные сплавы играют ключевую роль.